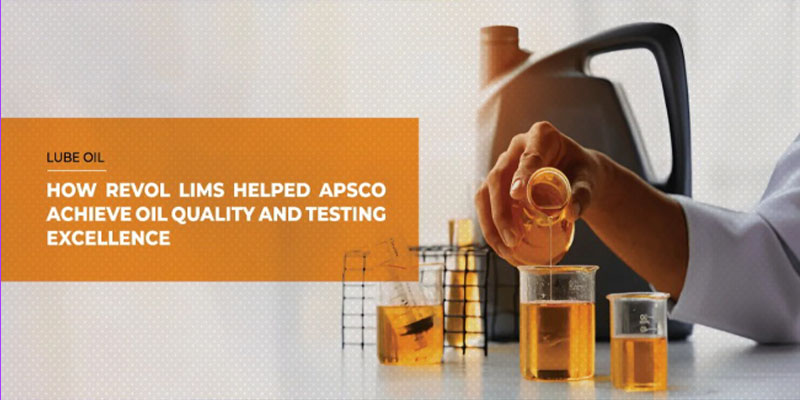
Abstract
APSCO is a prominent oil and gas company operating across the Middle East and Africa. Founded in 1973, the company aims to provide high-quality products and services to its customers in aviation, marine, and automotive industries.
APSCO offers a diverse range of products, including aviation fuel, lubricants, marine fuel, and gas station services, alongside offerings like oil analysis, quality control, and technical support. The company prides itself on innovation, excellence, and customer satisfaction, continually striving to distinguish itself from competitors by delivering exceptional value and performance.
Background
A significant contributor to APSCO's success is its advanced laboratory, which performs various tests and analyses on oil products to ensure quality and adherence to international standards. The laboratory processes thousands of samples each month from multiple sources and locations, employing cutting-edge instruments to conduct tests such as viscosity, density, flash point, and sulfur content.
Challenges
Despite having a well-equipped laboratory, APSCO faced several operational challenges:
Manual Processes and Errors: Manual data entry, measurement errors, and report preparation in various formats were consuming valuable time, resources, and money. Preparing and delivering test reports took an average of 3 days, with 10% of samples needing retesting due to human errors or instrument malfunctions. Additionally, storing test results in different formats like paper, Excel, or PDF made it difficult to retrieve and analyze data effectively.
Labor-Intensive Routine Testing: Laboratory staff were bogged down by repetitive tasks, limiting their ability to focus on analysis and innovation. Manual sample entry, instrument calibration, result transfer, and report generation consumed significant time and energy, while frequent customer inquiries added to their workload, impacting staff morale.
Need for a Streamlined Solution: APSCO required a laboratory management system to automate workflows, minimize errors, ensure compliance with ISO 17025, and streamline sample and data management. The solution also needed to offer value-added services like online access, real-time updates, and customized reports.
Solution
In search of a solution to automate workflows, integrate instruments, generate historical reports, and manage sample information, APSCO selected Revol LIMS. The system's cloud-based platform met APSCO’s needs at a competitive price point and provided the tools to enhance efficiency, accuracy, and customer service.
With Revol LIMS, APSCO gained a fully customizable, scalable system with comprehensive asset management and detailed test result tracking. Key features of the system included:
Online Portal for Customers: Customers can place test requests, track progress, and access previous orders and reports. APSCO processes samples on the same day and delivers custom reports, improving customer convenience and transparency.
Certificate of Analysis (CoA) Generation: APSCO can now generate and send branded CoAs in real-time, in multiple formats and languages, complete with logos, signatures, and additional customer-requested information.
Statistical Quality Control (SQC) and Comparison Charts: APSCO uses SQC and comparison charts to measure oil quality, track trends, and ensure compliance with industry standards such as ASTM, ISO, and API.
Results
Implementing Revol LIMS led to significant improvements in APSCO's laboratory operations and customer satisfaction:
Reduced Manual Processes and Errors: APSCO cut manual processes and errors by 80%. Automation streamlined data entry, validation, and reporting, reducing testing turnaround time from 3 days to 1 day and retesting rates from 10% to 2%.
Increased Efficiency: Integration with 18 instruments allowed automatic data transfer, reducing manual labor and speeding up the process. This boosted testing efficiency and turnaround times by 50%, delivering faster, more accurate results and enhancing customer satisfaction.
Improved Customer Service and Loyalty: The online portal, real-time updates, and customized reports increased transparency and engagement with customers, fostering trust and loyalty. Positive feedback and referrals led to higher customer retention and acquisition.
Enhanced Quality Control and Compliance: Using SQC charts, trend reports, and comparison charts, APSCO ensured oil quality met ISO 17025 standards. The data insights helped resolve issues and optimize testing methods, improving overall quality and safety.
Efficient Data Management: Revol LIMS' data import functionality enabled APSCO to manage historical data in one secure cloud database, saving 3 months of manual data entry. Customized forms for sample logging streamlined the process and reduced errors.
Automated Notifications: APSCO set up automatic email alerts for asset calibration and other maintenance activities, ensuring optimal equipment performance and minimizing downtime.
Quality Management System (QMS): Revol LIMS' QMS enhanced APSCO's quality management, helping maintain compliance, manage employee training, and track customer feedback and regulatory actions.
Conclusion
APSCO faced multiple challenges in laboratory operations, including manual processes, measurement errors, and regulatory compliance. Revol LIMS provided the ideal solution, automating workflows, integrating instruments, generating reports, and managing samples. The system also offered valuable services like online access and real-time updates, improving efficiency, quality, and customer satisfaction.
By adopting Revol LIMS, APSCO reduced manual processes by 80%, improved testing efficiency by 50%, enhanced customer service, and strengthened quality control and compliance. Revol LIMS transformed APSCO’s operations and contributed to their ongoing success.
Ready to achieve similar results? Contact us today for a free demo of Revol LIMS and discover how it can streamline your laboratory operations, boost productivity, and ensure quality.