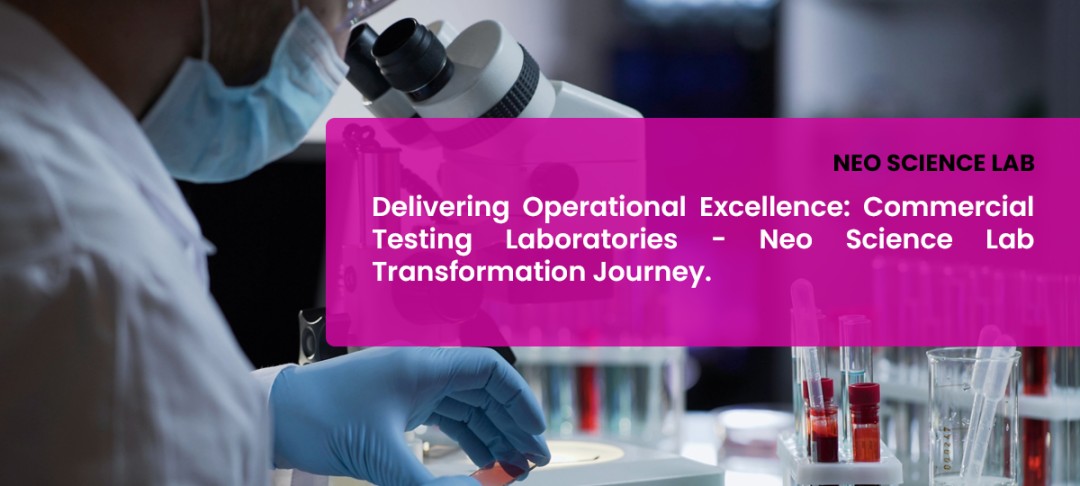
Abstract:
This case study highlights the transformative effects of implementing Revol LIMS at Neo Science Lab, a leading analytical testing facility in Chennai, India. Despite its advanced equipment and expert staff, Neo Science Lab faced numerous operational challenges, including inefficiencies in time management, inventory control, manual processes, client database handling, and calibration and maintenance tracking. To address these issues, Neo Science Lab adopted Revol LIMS, a cloud-based laboratory information management system, which digitized its operations, enhancing data management and improving workflow efficiency.
Key benefits included automated client and order management, comprehensive employee oversight, enhanced inventory control, and optimized maintenance and calibration processes. Following the implementation of Revol LIMS, Neo Science Lab saw a significant reduction in human errors, a boost in testing efficiency, and a marked increase in overall productivity. The lab also improved its quality control and compliance, achieving more accreditations and certifications. This case study illustrates how Revol LIMS played a key role in enhancing operational excellence at Neo Science Lab.
Background:
Neo Science Lab, located in Chennai, India, is a cutting-edge analytical testing laboratory. Established in 2016, the privately-owned facility is committed to delivering reliable, high-quality services. Specializing in analytical chemistry testing, Neo Science Lab handles everything from raw materials to finished products. The lab is fully accredited and environmentally conscious, focusing on scientific advancements, legal developments, and market growth. Its skilled team, specialized testing methods, accreditations, and commitment to minimal environmental impact set it apart within the industry. Neo Science Lab also collaborates with LQM labs for new method development and technology transfer.
The laboratory operates a diverse range of facilities, including microbiology, food, and pharmaceutical testing divisions. It follows national and international methodologies such as IS, FSSAI, APHA, AOAC, AOCS, CDFA, USP, IP, JP, E. Phur, and ISO, ensuring compliance with EPA, FDA, IMS, and USDA regulations. Neo Science Lab employs a variety of analytical techniques, including spectroscopy, physicochemical analysis, LCMSMS, GCMSMS, ICPMS, and GCHSS. The lab is also known for its custom and standard training programs, ensuring excellence in analytical testing and method development.
Challenges Faced:
Despite its advanced infrastructure, Neo Science Lab encountered several operational challenges that hindered its efficiency:
1) Time Management and Manual Processes: The lab’s reliance on manual methods for client and order management caused delays and workflow disruptions. This inefficiency resulted in significant time wastage, as each order required manual entry, verification, and tracking.
2) Data Storage and Sample Tracking: Manual storage and tracking of sample outcomes led to inaccuracies, often compromising the reliability of test results. These errors stemmed from human mistakes during data entry and retrieval processes, ultimately affecting the quality of test outcomes.
3) Order and Staff Management: Without an automated system, tracking orders and managing staff proved difficult. This led to lost orders, client confusion, and increased risk of malpractice due to insufficient oversight. Accountability and transparency within the lab were also challenges.
4) Calibration and Maintenance Issues: The manual tracking of calibration and preventive maintenance tasks resulted in instrument malfunctions, affecting operational continuity and quality control. Timely calibration and maintenance are critical for ensuring accurate and reliable test results, making this a major concern for the lab.
The Solution:
To address these challenges, Neo Science Lab implemented Revol LIMS, a cloud-based laboratory information management system designed to automate and streamline lab operations. Key features and benefits of Revol LIMS included:
Automated Client and Order Management: The system efficiently handles the entire client database and order tracking, eliminating manual errors and streamlining workflows. Clients can place orders online, which are then seamlessly managed by the system, significantly reducing processing time and errors.
Comprehensive Employee Oversight: Revol LIMS tracks employee attendance, leave, and payroll, automating these processes and preventing malpractice. This ensured real-time monitoring of staff activities, increasing accountability and reducing risks.
Enhanced Inventory Control: The system optimizes inventory management, reducing waste and ensuring the lab has the necessary materials without overstocking. Real-time updates on stock levels allowed for better planning and procurement.
Streamlined Calibration and Maintenance: Revol LIMS automates the tracking of calibration and preventive maintenance tasks, ensuring instruments are always in optimal condition. Maintenance activities are scheduled in advance, minimizing downtime and ensuring quality control.
Customizable Reporting: The software generates reports in multiple formats (Word, Excel, PDF), improving data accessibility and ensuring compliance with regulatory standards. This feature facilitated easy report preparation for clients and regulatory bodies, ensuring transparency and compliance.
Impact:
The implementation of Revol LIMS led to several significant improvements at Neo Science Lab, including:
Reduction in Manual Processes and Errors: Automation minimized manual intervention, reducing errors and malpractice. This streamlined workflow improved data management accuracy, allowing lab staff to focus on core tasks and enhancing overall productivity.
Better Inventory and Instrument Management: Efficient inventory control and proactive maintenance ensured operational continuity and minimized losses. Real-time inventory updates and automated maintenance schedules reduced unexpected downtimes and delays.
Improved Workflow and Efficiency: Streamlined processes enhanced staff productivity and testing efficiency, enabling the lab to process more samples within tight deadlines. This resulted in faster turnaround times and increased client satisfaction and retention.
Enhanced Quality Control and Compliance: Improved adherence to protocols and the adoption of ISO 17025 methods bolstered quality and compliance, earning Neo Science Lab additional certifications and accreditations. This strengthened the lab’s reputation and credibility, creating new business opportunities.
Conclusion:
The implementation of Revol LIMS revolutionized Neo Science Lab's operations, transforming inefficiencies into streamlined workflows. By automating client management, employee oversight, inventory control, and maintenance, Revol LIMS reduced human errors, enhanced productivity, and improved client satisfaction. Analytics and dashboards within the system enabled better decision-making, leading to significant cost savings, improved quality control, and ensured compliance with regulatory standards. With more accreditations and certifications, Neo Science Lab is poised for growth and expansion. Revol LIMS has become the backbone of the lab's operations, supporting its continued success.
Ready to transform your laboratory operations? Discover how Revol LIMS can streamline processes, boost productivity, optimize workflows, and uphold the highest quality standards. Contact www.revollims.com today to experience the benefits of our state-of-the-art laboratory information management system.